Case Study 1: One of the World’s Largest Oil Plants
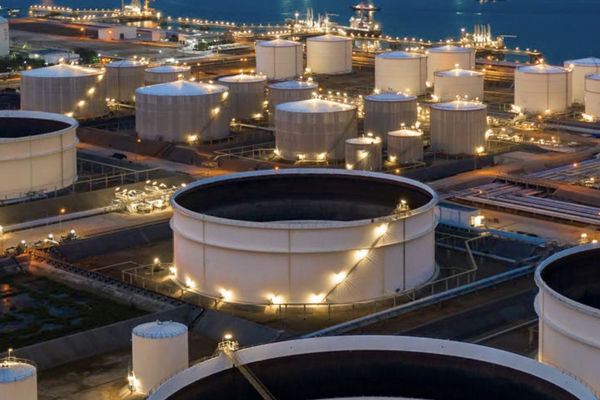
- The Problem
- How to unify and effectively utilize the vast amount of information?
- Solution
- Thorough digital shift, cloud computing.
Data and metadata connectivity, synchronization of data from 40 countries around the world.
Data visualization, organization, and analysis.
Case Study 2. Electric power company in North America
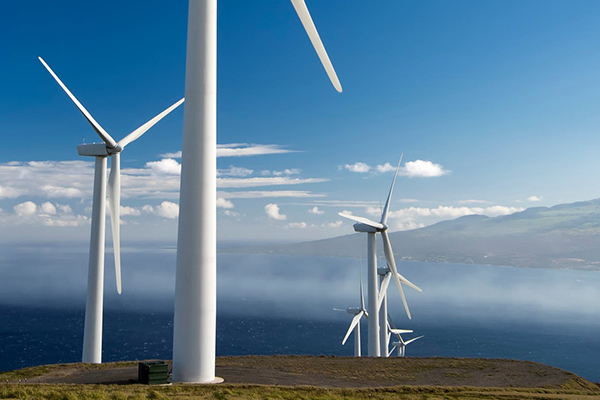
- Problem
- Management of 23,000 wind turbines from different manufacturers.
3,000 data points every 10 minutes.
(Over 50 billion data points per year)
- Solution.
- Cloud-based data management and analysis.
Case Study 3. Spinning mill
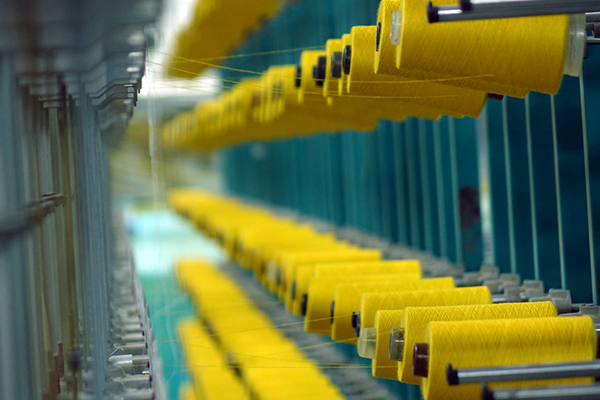
- Problem
- Manufacturing problems due to outdated data collection and human error.
- Solution
- Connectors, Fusion, Lenses, Trackers™ Trackers™: track equipment malfunctions and why.
Case Study 4. Logistics (Rail)
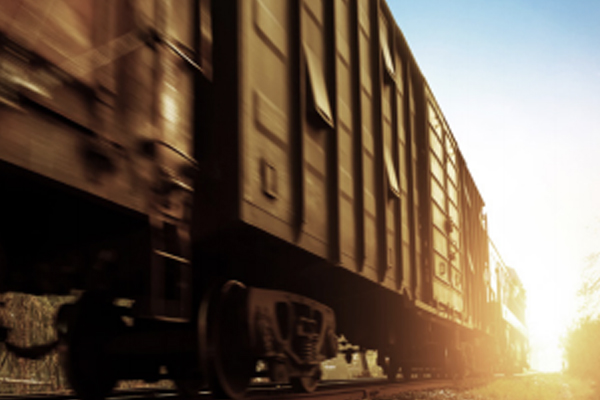
- Problem
- Significant cost and schedule impact due to post-failure response.
- Solution
- Management through standardization of data and unification of content ASL Explorer™: Advance maintenance arrangements based on collected data. Prevent major breakdowns with small maintenance.
Case Study 5. Nuclear power plant
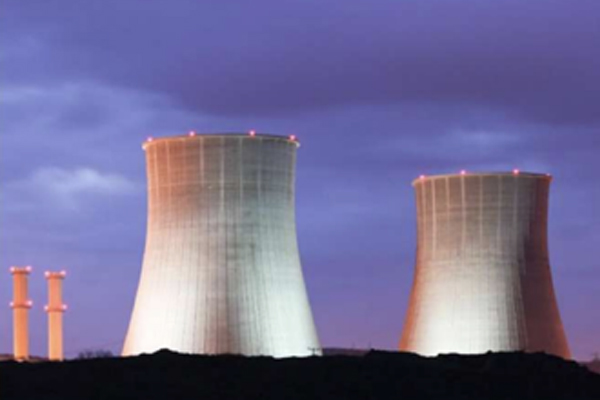
- Problem
- Improvement of situation requiring maintenance costs beyond budget and schedule.
- Solution
- Analyzed over 600 data trends. Proposed effective alternatives while maintaining safety and reliability. Reduced labor hours by 1,660. Material cost savings of $187,000 (approx. 20 million yen). Power generation loss: $313,000 (approx. 35 million yen) saved.
Case Study 6. Logistics (trucks)

- Problem
- From an environmental standpoint, from diesel to compressed natural gas Adapting to new technology and unforeseen cost increases.
- Solution
- Adapted a model from Uptake’s Digital Industry Library Analyzed existing data with the model to predict engine problems with a 90%+ rating and scheduled repairs to reduce downtime. During the initial four months, the model was adapted to save approximately 80 units.
Case Study 7. Logistics (trucks)
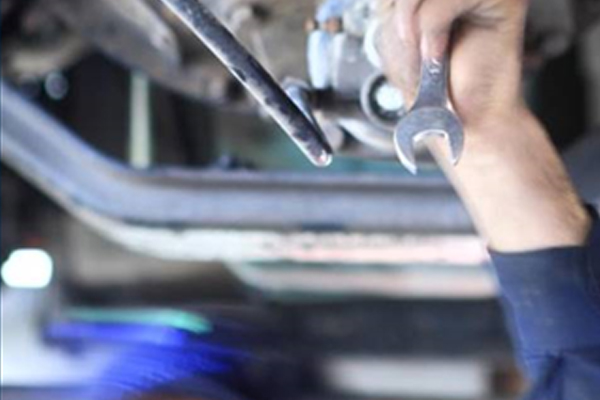
- Problem
- Maintenance strategy for 1,000 trucks in various logistics areas: Average repair cost $1,200/day, additional driver cost $8,000/day.
- Solution
- Predicted breakdowns based on current vehicle data and historical work. 29 breakdowns were predicted from all vehicles in operation in the U.S. and compared to historical data of actual breakdowns to save $3,387/year per vehicle through early breakdown countermeasures.
Questions, concerns, etc.
Feel free to contact us 24 hours a day, 7 days a week, 365 days a year!
For more specialized AI business inquiries, please contact AASC’s cutting-edge AI business experts